Organisations are constantly on the hunt for innovative solutions to streamline processes, improve operational efficiency, and cutting costs. One approach gaining significant momentum is the adoption of artificial intelligence (AI) in monitoring and maintaining machinery and equipment. This is the era of predictive maintenance, where AI not only foresees potential failures but also enables real-time optimisation of maintenance tasks.
What is Predictive Asset Maintenance?
Predictive maintenance is a forward-looking strategy that uses AI and data analytics to forecast when equipment is likely to fail or require maintenance. Unlike traditional reactive or routine scheduled maintenance, predictive maintenance emphasises anticipating and preventing issues before they disrupt operations.
The AI Advantage in Predictive Maintenance
- Real-Time Monitoring and Insights
Traditional maintenance approaches rely on periodic manual checks, which can overlook subtle variations in machine performance. AI-powered systems, on the other hand, provide continuous monitoring of equipment, analysing vast data streams in real time. By detecting minor anomalies or deviations from standard operating conditions, these systems can flag potential issues long before they escalate. - Cost Efficiency
Unplanned downtime can be financially crippling, leading to lost productivity, emergency repair costs, and missed deadlines. Predictive maintenance mitigates these risks by identifying problems early, reducing the likelihood of expensive equipment failures. - Extended Equipment Lifespan
Timely maintenance based on AI insights can significantly extend the life of machinery and equipment. This not only ensures a better return on investment but also delays the need for costly replacements. - Enhanced Quality and Safety
By ensuring machinery operates at optimal levels, predictive maintenance improves production quality. Moreover, identifying and addressing potential breakdowns reduces the risk of workplace accidents, fostering a safer working environment. - Optimised Resource Allocation
AI-driven predictions enable maintenance teams to be more strategically deployed. With accurate forecasts, teams can ensure they have the necessary tools and spare parts, minimising resource wastage and boosting efficiency.
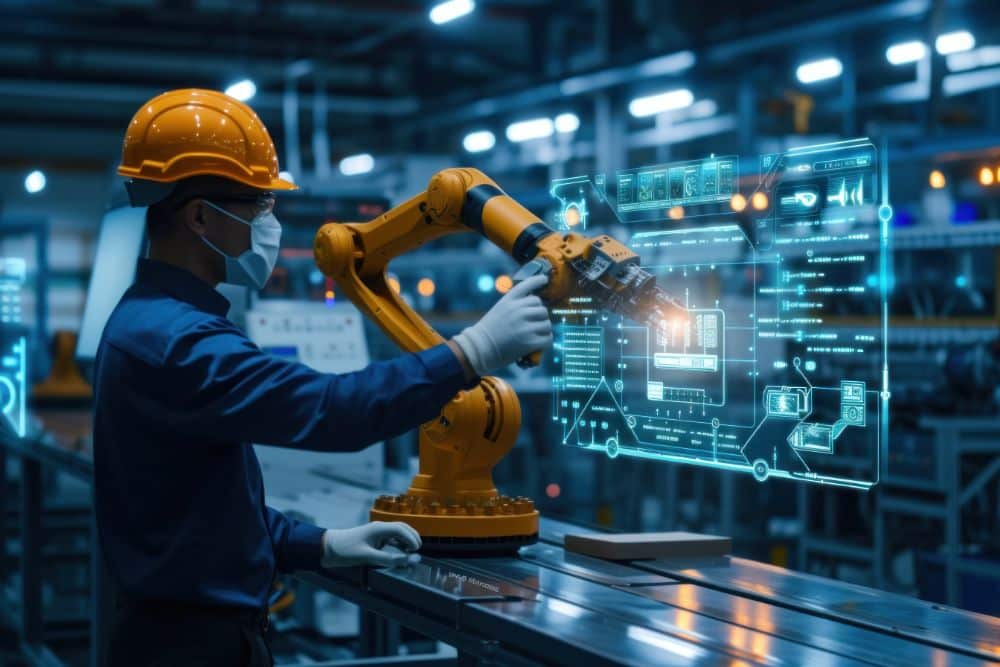
How AI Powers Predictive Maintenance
- Data Collection
AI-driven predictive maintenance relies on real-time data gathered by IoT (Internet of Things) sensors installed on the equipment. These sensors capture critical parameters such as vibration, temperature, and noise levels. - Data Processing and Learning
AI algorithms process this data to understand the normal operational behaviour of machinery. By continuously learning, these systems can establish benchmarks for optimal performance. - Anomaly Detection
Over time, the AI system identifies deviations from the established norms. These anomalies often serve as early indicators of potential issues, allowing for timely intervention. - Predictive Analysis
By combining historical and real-time data, AI predicts when equipment is likely to require maintenance or face a failure, enabling organisations to act pre-emptively.
Bridging AI with Maintenance Strategies
AI enhances and integrates seamlessly with various maintenance strategies, improving their effectiveness:
- Corrective Maintenance
This reactive approach involves addressing anomalies once they are detected. AI augments this strategy by identifying and diagnosing issues more quickly, reducing downtime. - Preventive Maintenance
AI improves traditional preventive measures, which rely on pre-scheduled maintenance intervals. By analysing real-time data, AI helps refine these schedules, ensuring maintenance is performed only when genuinely needed. - Risk-Based Maintenance
Risk-based maintenance involves analysing environmental, operational, and process conditions to determine maintenance priorities. AI streamlines this by continuously collecting and processing relevant data, offering dynamic risk assessments. - Condition-Based Maintenance
This strategy bases maintenance on real-time equipment performance monitoring. AI plays a pivotal role here by continuously assessing device conditions through IoT data. Maintenance is triggered only when specific performance indicators suggest deterioration, drastically reducing costs and preventing significant faults.
Sensor Data Intelligence for Microsoft Dynamics
AI solutions like Sensor Data Intelligence integrate with platforms such as Microsoft Dynamics 365 Supply Chain Management to enhance predictive maintenance capabilities. Here’s how Sensor Data Intelligence transforms operations:
- Seamless Data Integration: IoT sensors capture machine data and update asset counters directly within the supply chain management system.
- User-Friendly Onboarding: Organisations can set up the system with an intuitive wizard, eliminating the need for complex manual installations.
- Customisable Azure Components: Businesses retain full control over Azure components, allowing them to scale and adapt the solution to their specific needs.
- Proactive Maintenance: By leveraging IoT signals, organisations can predict maintenance needs, improving both efficiency and reliability.
The Future of AI-Driven Predictive Maintenance
The integration of AI into maintenance strategies represents a significant shift in how organisations manage the health of their machinery and equipment. Emerging trends and advancements are set to make predictive maintenance even more impactful:
- Edge Computing
AI algorithms are increasingly being deployed at the edge, directly on IoT devices. This minimises latency, allowing for faster anomaly detection and predictive insights. - Enhanced Machine Learning Models
As AI models become more sophisticated, they’ll be able to process even more complex datasets, improving the accuracy and reliability of predictions. - Cross-System Integration
Future AI solutions will integrate seamlessly across multiple business systems, from supply chain management to customer service, creating a unified digital ecosystem. - Autonomous Maintenance
AI could enable machinery to autonomously perform minor repairs or adjustments, further reducing the need for human intervention.
Embracing Predictive Maintenance
Organisations that adopt AI-driven predictive maintenance not only reduce costs but also gain a competitive edge by improving efficiency, safety, and equipment reliability. This proactive approach positions businesses as industry leaders, ready to embrace the challenges and opportunities of the digital age.
Explore how Intelisense can help you unlock the potential of AI-powered predictive maintenance and revolutionise your operations. Contact us today to learn more.