Embracing Digital Transformation in Manufacturing
Digital transformation in manufacturing has become crucial for large-size companies and industries aiming to stay competitive and innovative. Leveraging progressive technologies such as IoT, Digital Twins, and advanced data management systems is key to achieving operational excellence and driving future growth. Here’s how technical integrations and data management are shaping the future of manufacturing in 2024.
The Imperative of Digital Transformation
Digital transformation in manufacturing isn’t merely about adopting new technologies; it involves a holistic approach to integrating digital capabilities into all aspects of operations. This transformation encompasses leveraging data analytics, automation, artificial intelligence (AI), cloud computing, and other emerging technologies to drive efficiency, innovation, and customer-centricity.
Key Benefits:
- Enhanced Operational Efficiency: Automation and AI streamline production processes, reducing human error and operational costs.
- Optimised Supply Chains: Real-time data analytics enable better supply chain management, reducing delays and enhancing inventory control.
- Personalised Customer Experiences: Advanced data analytics help in understanding customer needs and tailoring products accordingly.
- Data-Driven Decision Making: Robust data management systems allow for informed decision-making based on accurate, real-time data insights.
Technical Integrations in Manufacturing
- Internet of Things (IoT): IoT enhances the manufacturing sector by providing real-time insights into machinery and processes. By connecting devices and systems, manufacturers can monitor operations remotely, predict maintenance needs, and optimise production lines.
- Digital Twins: A Digital Twin is a virtual replica of a physical product or system. This technology allows manufacturers to simulate, predict, and optimise the performance of their products and processes. Digital Twins help in improving product designs, troubleshooting issues before they occur, and enhancing the overall efficiency of manufacturing operations.
- Cloud Computing: Migrating to cloud-based solutions offers numerous benefits, including scalability, cost efficiency, and enhanced data security. Cloud platforms like Microsoft Azure and Business Applications solutions such as Dynamics 365 provide robust infrastructure for managing manufacturing operations and integrating various digital tools seamlessly.
Data Management Strategies
Effective data management is the backbone of digital transformation. It involves collecting, storing, and analysing data to extract actionable insights that drive business decisions.
- Data Maturity Assessment: Assessing the maturity of an organisation’s data practices is essential. This involves evaluating data governance, data quality, and analytical capabilities to ensure the organisation can leverage its data effectively.
- Data Transformation: Transforming raw data into meaningful insights requires advanced analytics and machine learning algorithms. Tools like Microsoft PowerBI help in visualising data, making it easier for decision-makers to understand complex information quickly.
- Integration of AI and Machine Learning: Incorporating AI and machine learning into data management systems can significantly enhance predictive analytics, enabling manufacturers to foresee market trends, optimise operations, and improve product quality.
Cloud-based Solutions
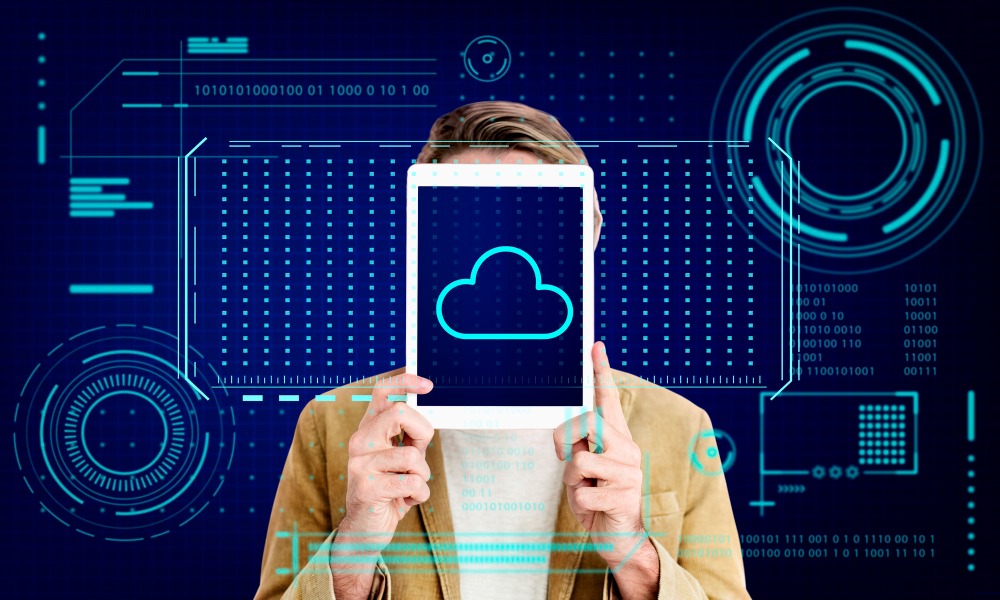
Digital Transformation Free Workshops
To support customers’ growth, Intelisense offers bespoke workshops designed to eliminate uncertainty and risk for organisations ready for change. These workshops help plan a successful transformation to an enhanced digital landscape, laying a solid foundation for sustainable growth and a future-proof system infrastructure.
FAQ's
A digitalisation strategy for manufacturing involves using digital technology to enhance various aspects of production. This strategy focuses on automating processes, improving communication, and utilising data analytics to boost efficiency and productivity.
Key focus areas include:
- Automation: Implementing robotics and automated systems.
- Data Analytics: Leveraging big data for better decision-making.
- Supply Chain Optimisation: Enhancing logistics with technology.
- Worker Safety and Training: Using tech to improve safety and skill.
Digital transformation integrates technology into every facet of manufacturing, from the supply chain to the factory floor. It uses sensors, data analytics, and interconnected machinery to streamline operations and adapt to market demands swiftly.
These are four challenges of digital transformation in manufacturing:
- Investment Costs: High initial expenses for technology acquisition.
- Security Concerns: Increased risk of data breaches.
- Skill Shortages: Need for staff with advanced digital skills.
- System Integration: Challenges in integrating new technologies with legacy systems.